The first one started quite a while ago and got completly sidetracked.
Still working on an electric
wire stripper that just smashes the insulation and the copper falls out.
I bought this jewelers wire mill. It is manual crank. 2.25 revolutions of crank turms the rollers one revolution.

Very slow so I decided to add a motor. As a scrapper I was given two of these. Both have parts missing but the motors work.
I pulled one motor and bought two pullies and a belt to connect the mill to the motor.
The motor is 1750 RPM and with the pullies and then the gears I believe I get the rollers to go about 350 RPM still way too fast and the gears make a racket.
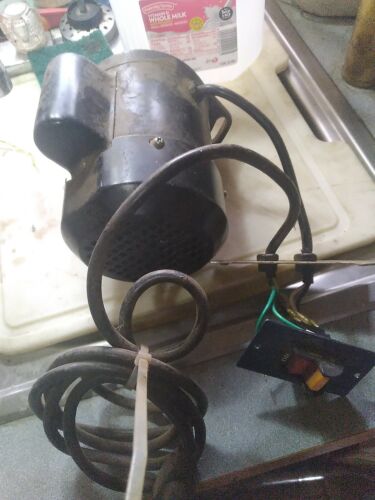
I want to reduce the speed much more. I bought this varible speed govenor on
amazon. They even advertised that it would be good for woodworking equipment. It did not work at all to slow down the motor.
So this is where I am at now. Does the capaciter start have anything to do with it not slowing down.?
Any opinions on what to get?
None of these photos are mine. all borrowed off the internet. This forum will still not let me upload any photos.
Bookmarks